Starting with Initial Models into Final Output: The Role of Conductive Rods Made of Polyimide
In the constantly changing landscape of materials engineering, electrically conductive polyimide rods are carving out a considerable niche for themselves. These high-performance components are capturing the attention of sectors that demand reliability and performance, particularly in applications where heat management and electric conduction are critical. As https://www.hsjuxin-pi.com/category/products/polyimide-rod/ shift from the initial designs of development into large-scale manufacturing, comprehending the advantages and functionalities of conductive polyimide resin rods becomes essential.
The aerospace industry, known for its rigorous standards and challenging environments, can greatly benefit greatly from the use of these innovative materials. Conductive polyimide rods not only satisfy the demanding requirements for mass and strength but also excel in their ability to withstand high temperatures and oxidative conditions. As creators and designers seek to improve their designs, the adoption of these rods can lead to improved functionality and longevity in aerospace applications, ultimately leading to more secure and optimized flight systems.
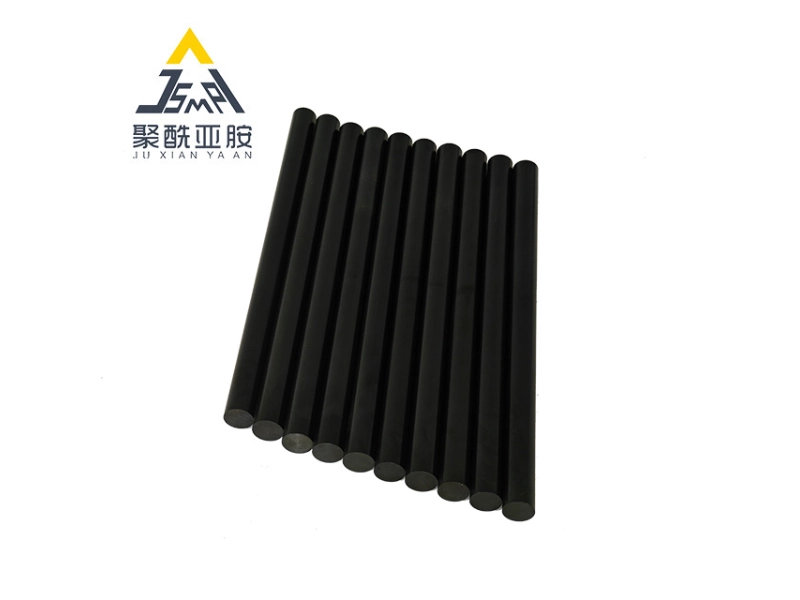
Features of Conductive Polyimide-Based Rods
Conductive polyimide rods are well-known for their outstanding thermal stability, which makes them ideal for demanding applications, especially in the aerospace industry. These rods can preserve their integrity and performance under severe temperature fluctuations, ranging from -269 degrees Celsius to over 300 degrees Celsius. This property is vital for components that operate in hostile environments, ensuring durability and longevity in aerospace applications.
Moreover, notable characteristic of conductive polyimide rods is their excellent electrical conductivity. Unlike traditional polyimides, the addition of electrical fillers enhances their ability to conduct electricity while still retaining the benefits of polyimide resin, such as structural strength and chemical resistance. This twofold functionality makes them ideal for use in various electronic components, providing the necessary conductivity without compromising on structural integrity.
In addition, these rods exhibit superb mechanical properties, including high tensile strength and flexibility. This strength allows them to endure various stressors encountered during manufacturing and in operational settings. The combination of superior attributes ensures that electrically conductive polyimide rods can be molded into intricate shapes required in prototypes and final production parts, making them a popular material in cutting-edge technology development.
Applications in Space Industry
Conductive polyimide rods are growing traction in the space industry due to their singular combination of low-weight properties and high thermal stability. These rods are essential components for diverse applications including insulation and electrical interconnections in aircraft platforms. Their ability to endure extreme temperatures while maintaining functionality makes them ideal for key aerospace components that require reliable operation in demanding environments.
In addition to their structural applications, conductive polyimide rods serve a significant role in the development of advanced aircraft systems. The aviation sector stresses the need for materials that not only meet strict safety standards but also enhance to energy efficiency. With their superior electrical insulation properties and low-weight characteristics, these high-performance polyimide rods are optimal for use in avionics and connectivity systems, enhancing total system performance while reducing weight.
Furthermore, the inclusion of conductive polyimide rods in aerospace design allows for creative engineering solutions. Their versatility enables designers to create more smaller and effective systems, such as integrated sensor packages and multifunctional components. As the aviation industry continues to push towards more green and state-of-the-art technologies, the reliance on materials like conductive polyimide rods will certainly increase, laying the way for the future of aircraft design.
Commencing at Initial Models and Full-Scale Production
Moving away from prototypes to production through the creation of conductive polyimide rods stands as a crucial aspect which determines the substance's performance in real-world uses. In the early prototype phase, engineers and designers examine the viability of using advanced polyimide rods, testing different compositions and configurations. This exploration allows for adjustments in properties such as electric conductivity, adaptability, and thermal resistance, ensuring that the end product satisfies defined requirements for challenging applications.
While production processes get refined, expanding production becomes a key area of concern. The aerospace industry, especially, requires materials that are able to withstand harsh conditions and maintaining operational integrity. Electrically conductive polyimide rods have been used in this sector due to their low weight nature and superior mechanical properties. The capacity to manufacture these rods in mass and maintaining product quality becomes essential, as even small inconsistencies in material performance might lead to serious issues in aerospace applications.
After the production process has been optimized, the emphasis moves to quality control and adherence with industry standards. Conductive polyimide rods need to go through thorough testing to ensure they satisfy the strict regulations established by aerospace authorities. This consists of thermal cycling, mechanical stress testing, and tests for electrical conductivity. Successful validation opens the way for large-scale production, enabling the widespread use of these cutting-edge materials, that not only boost performance while also increase the general reliability of aerospace systems.
Upcoming Trends in Polyimide-based
As the requirement for high-performance materials grows, the future of polyimide looks bright. Developments in the manufacture of conductive polyimide rods are expected to boost their applications across various sectors, especially in aerospace. With ongoing studies focused on improving heat resistance and physical characteristics, advanced polyimide rods may become even more effective in harsh environments, paving the way for their application in high-tech aerospace systems.
The incorporation of smart materials and coatings into polyimide technology will also take a significant role in the advancement of these rods. By incorporating sensors or self-healing capabilities, conductive polyimide rods can become multifunctional, offering not only structural support but also innovative surveillance and maintenance capabilities. This development will be notably beneficial in the aerospace industry, where security and reliability are of utmost significance.
In addition, the trend toward eco-friendliness in production will affect the creation of polyimide materials. Researchers are exploring bio-based precursors and sustainable processing techniques, aiming to reduce the environmental impact of polyimide synthesis. As the industry shifts towards greener operations, the development of sustainable conductive polyimide rods could lead to broader adoption and application in various sectors, ensuring that these materials remain at the leading edge of innovation.